Turbo Tel's pictures
Mar 30th, Schedule 40 pipe Manifold
I found a Free CAD program at http://www.emachineshop.com/ and found it really useful, at the bottom of this page I (will) have links to download my designs. First I drew up my
turbo and manifold flanges Then I converted in a drawing of my GT15 turbo, split the compresssor off and was able to spin and arrange the turbo to my hearts content.
Then I measured and drew up the profile of the available area behind the engine. I found that a good angle for the turbo was with it at 45 degrees, this was nice as
it keeps the design simple,and I found that by using 1-1/4" Shedule 40 pipe. Tee and short radius elbows I could make this work.... as long as I use an n/a inlet manifold, the turbo manifold is just too difficult.
The initial idea was to use a "T" with a shortened leg and two short link pipes with short radius elbows at the end. The final piece was some short raduis 90's cut in half to get the manifold tilted at the 45 degrees needed.
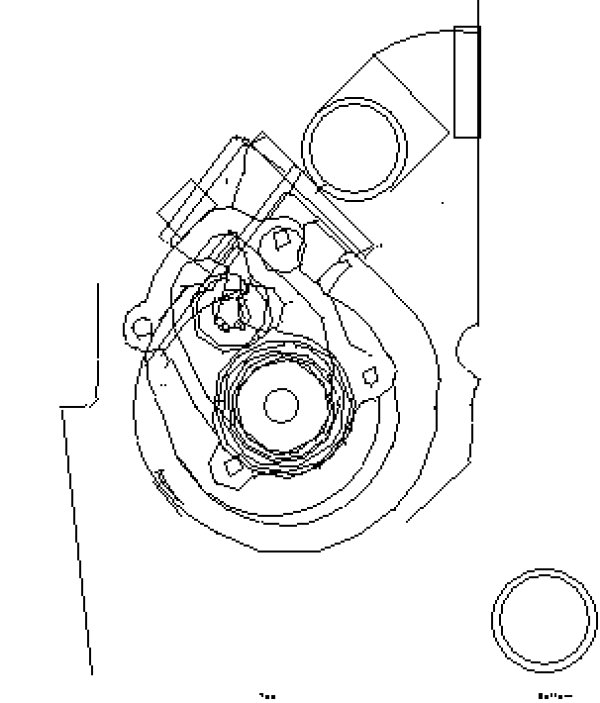
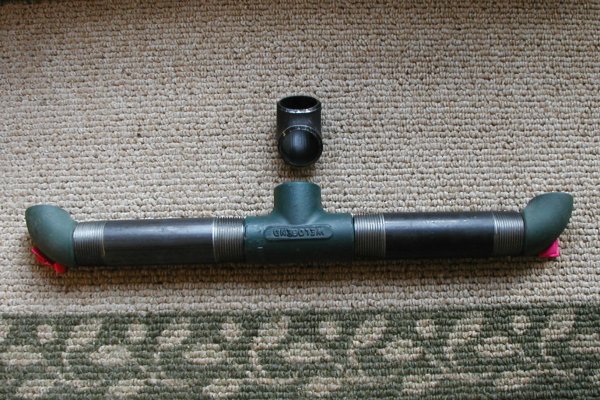
Later on I looked at using long radius elbows to help the flow but just could not fit them in, then I realised that it doesn't have to be straight, and using the CAD I realised that I could use the long radius
elbows If I angled the link pipes, It came out at 15 degrees.
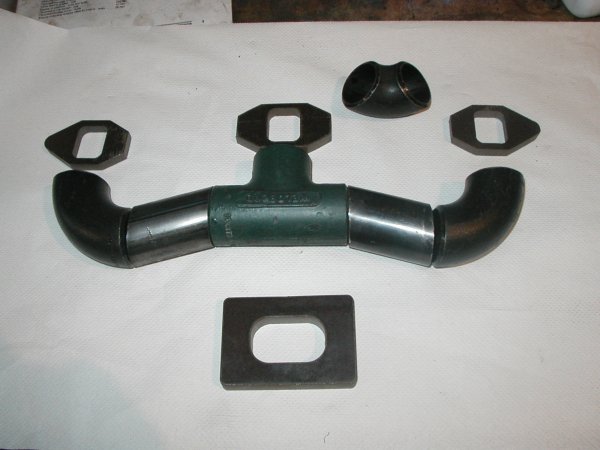
Next was to test out the theory, I printed up the manifold design and taped it to the turbo and arranged it up with the carbs, Everything looked great but I had a slight
problem with the outlet of the turbo. If I pointed it up the normal way There was nowhere to mount the actuator.. lots of extra work. However If I point it down the actuator will actually fit, all I need is to
drill/tap one extra hole in the compressor. Pointing it down gives extra problems with the piping but as I am going to have an intercooler eventually Its not as bad. The other problem was how tight the oil drain was
with the outlet right next to it but a days worth of fiddling with the CAD program and I had that cracked as well.
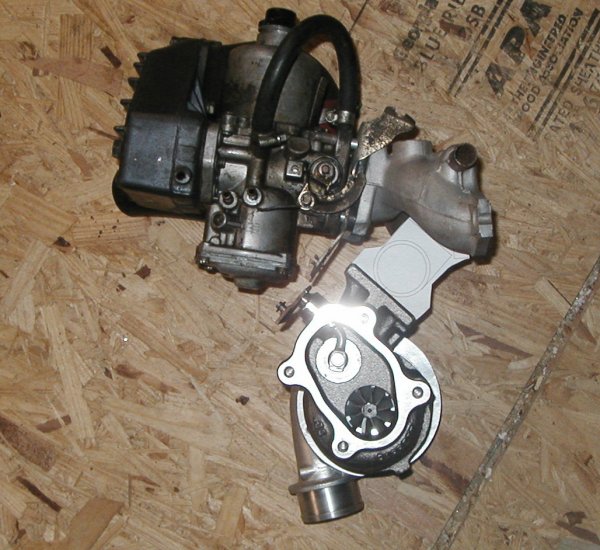
Started the fabrication, I used my 10" mitre saw with an abrasive wheel to cut the 15 degree 1-1/4 pipe sections It worked fine aside from the plastic shield catching fire!! I then offered them up and they fitted exactly as planned--centred on the ports but... when offering them up I
realised that the pipes would foul the nuts at each end of the manifold so I would have to shorten them a bit to give clearance for the nuts, I ended up with 54mm sections. I then welded them up to the "T" and tidied the joints.
Thankfully my welds look fine, must be getting better!! I now need to grind/tidy up the joints on the inside to avoid hotspots before welding on the elbows.
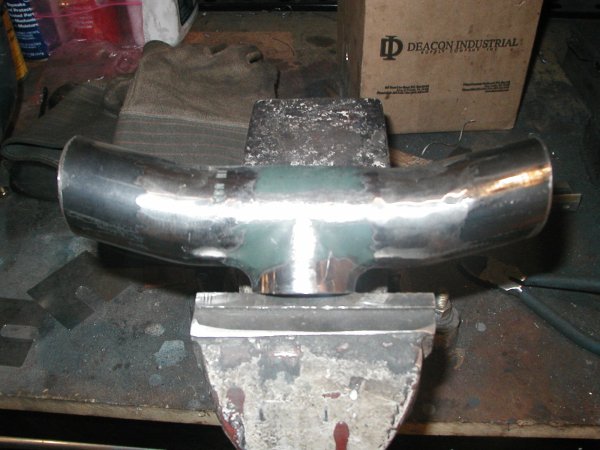
My welding, though not the best, is definitely getting better!!.
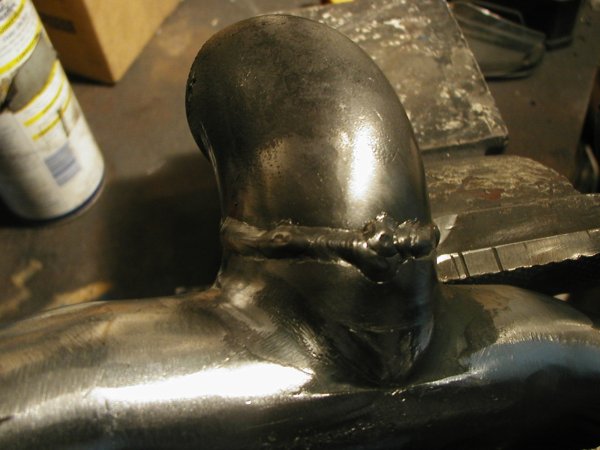
Phase one complete, Off to the Machine shop to get the ends cut to 45degrees and the centre cut to take the Turbo flange.
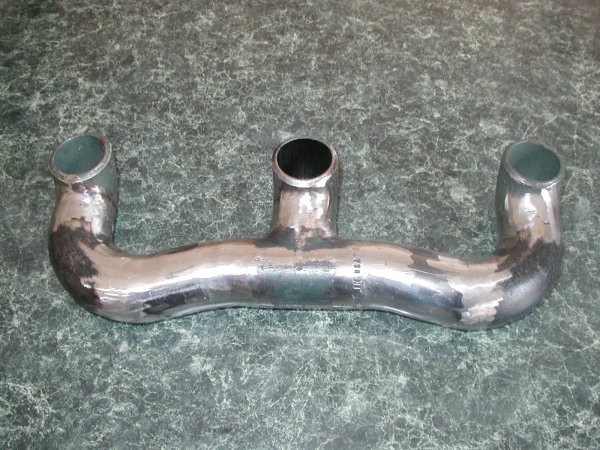
6 Weeks later.... All the machine shop managed was to cut the angles...Incorrectly. I'm back to square one and having trouble getting someone to bother over such a small job. I'm just lost for words over the way they have treated me I dont think I deserved it after having them do all 3 of my engines over the last 10 years. .
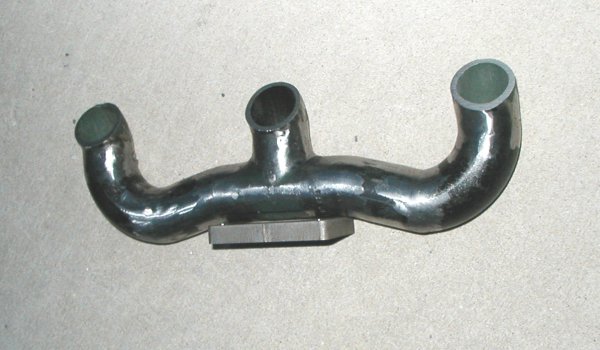
Back to engine page